The Future of Manufacturing: Digital Twins as the Cornerstone of Industry 4.0
As we stand on the brink of the Fourth Industrial Revolution, commonly known as Industry 4.0, the manufacturing landscape is undergoing a transformative shift. This new era is characterized by the integration of advanced technologies, such as the Internet of Things (IoT), artificial intelligence (AI), and big data analytics, to create smarter, more efficient manufacturing processes. At the heart of this revolution lies a groundbreaking concept: Digital Twins.
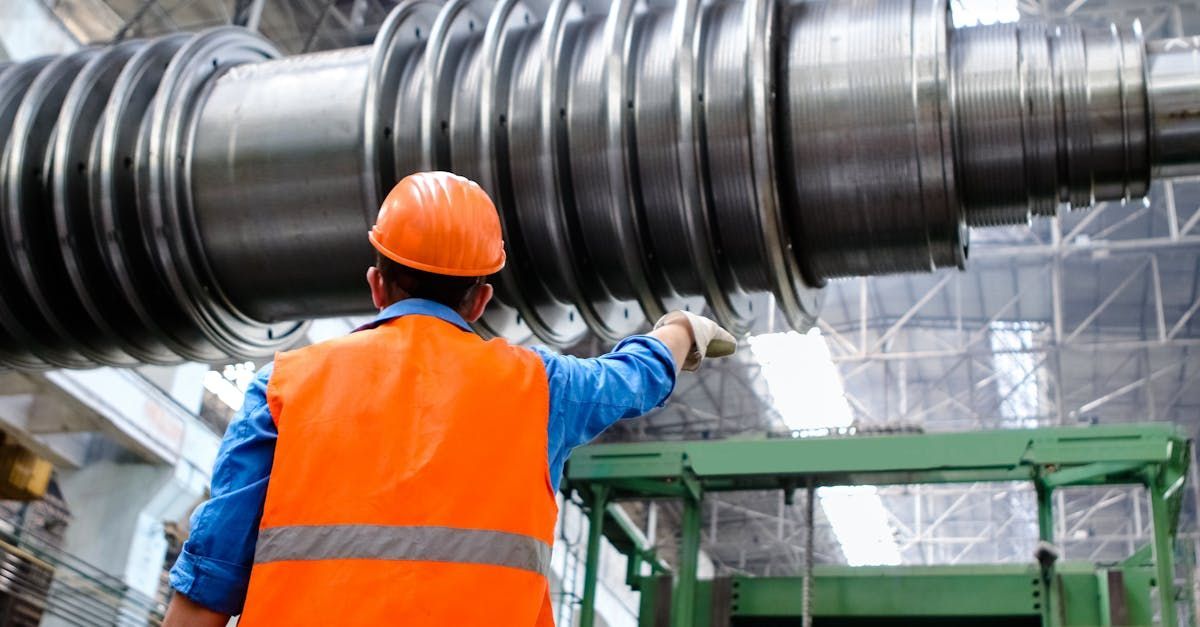
What Are Digital Twins?
Digital Twins are virtual replicas of physical assets, systems, or processes. These sophisticated models use real-time data to mirror and simulate the behavior and performance of their physical counterparts. By creating a digital counterpart for every physical entity, businesses can gain unprecedented insights into their operations, predict outcomes, and optimize performance.
The Role of Digital Twins in Industry 4.0
In the context of Industry 4.0, Digital Twins serve as a crucial component, enabling the seamless integration of the physical and virtual worlds. This integration allows for the creation of intelligent factories where data-driven production and decision-making become the norm. Here’s how Digital Twins are reshaping the manufacturing industry:
1. Enhanced Data Integration and Analysis
Digital Twins aggregate data from various sources, including sensors, IoT devices, and enterprise systems. This comprehensive data integration facilitates a holistic view of the manufacturing process, enabling manufacturers to analyze and interpret data in real-time. As a result, businesses can make informed decisions, identify patterns, and uncover opportunities for improvement.
2. Simulation and Optimization
With Digital Twins, manufacturers can simulate different scenarios and test the impact of various changes without disrupting actual operations. This capability allows for the optimization of production processes, reducing downtime, enhancing efficiency, and minimizing waste. By experimenting in the virtual realm, businesses can find the best possible solutions for their physical operations.
3. Predictive Capabilities
One of the most powerful features of Digital Twins is their predictive capabilities. By analyzing historical and real-time data, Digital Twins can forecast future outcomes and identify potential issues before they arise. This foresight enables manufacturers to proactively address challenges, ensuring smoother and more reliable operations.
4. Enhanced Collaboration and Communication
Digital Twins foster enhanced collaboration and communication among different stakeholders. Engineers, operators, and decision-makers can interact with the digital model, share insights, and collaborate on solutions. This collaborative approach breaks down silos, promotes knowledge sharing, and drives continuous improvement.
Nimbus XP: Leading the Industry 4.0 Revolution
At Nimbus XP, we are at the forefront of the Industry 4.0 revolution, championing the adoption and implementation of Digital Twin technology. Our expertise in digital twin modeling platforms and consulting services positions us as leaders in this transformative era. We empower businesses to harness the full potential of Digital Twins, driving innovation, efficiency, and competitiveness in the manufacturing sector.
Conclusion
As Industry 4.0 continues to evolve, Digital Twins will remain a cornerstone of this revolution, bridging the gap between the physical and virtual worlds. By enabling data-driven production, predictive capabilities, and enhanced collaboration, Digital Twins are set to redefine the future of manufacturing. Nimbus XP is proud to be a leader in this space, guiding businesses towards a smarter, more efficient, and innovative future.
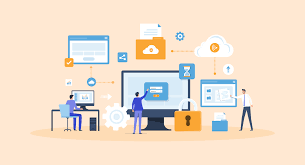
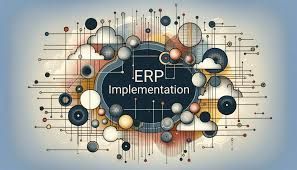
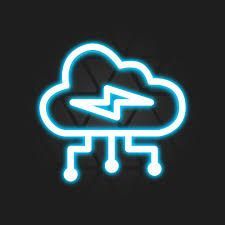
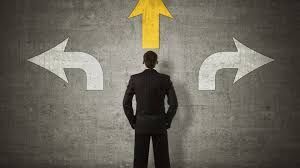
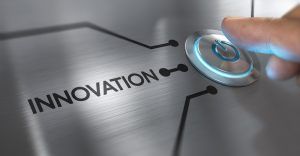
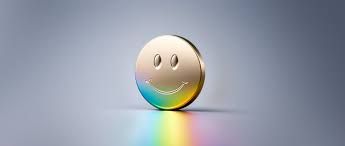